Model Selection
9200-AA-BB-CC-DD | |||
AA: Transducer Mounting Angle/Minimum Operating Frequency Option | |||
01 | 0±2.5, 4.5 Hz (270 cpm) | 06 | 0±100, 10 Hz (600cpm) |
02 | 45±2.5, 4.5 Hz (270 cpm) | 09 | 0±180, 15 Hz (900 cpm) |
03 | 90±2.5, 4.5 Hz (270 cpm) |
|
|
BB: Connector / Cable Option | |||
01 | Top Mount (no cable) | 05 | Terminal block top mount (no Cable) |
02 | Side Mount (no cable | 12 | Miniature coaxial ClickLoc connector, FluidLoc cable |
10 | 10 feet (3.0 meter) | 15 | 15 feet (4.6 meter) |
22 | 22 feet (6.7 meter) | 32 | 32 feet (9.8 meter) |
50 | 50 feet (15.2 meter) |
|
|
CC: Mounting Base Option | |||
01 | Circular; 1/4-20 UNC stud | 07 | Isolated circular 1/4-28 UNF stud |
02 | Circular; 1/4-28 UNF stud | 08 | Isolated rectangular flange |
03 | Rectangular flange | 09 | Isolated circular 5/8-18 UNF stud |
04 | Circular; with three 8-32 threaded studs on a 44 mm (1.75 in) diameter bolt circle | 10 | Circular; M10X1 stud |
05 | No base; 1/2-20 UNF-3A stud | 11 | Isolated circular M10X |
06 | Isolated circular 1/4-20 UNC stud | 12 | Isolated circular 1/2-20 UNF-2A |
DD: Agency Approval Option | |||
00 | No Approvals | 04 | ATEX/IECEX |
01 | CSA |
|
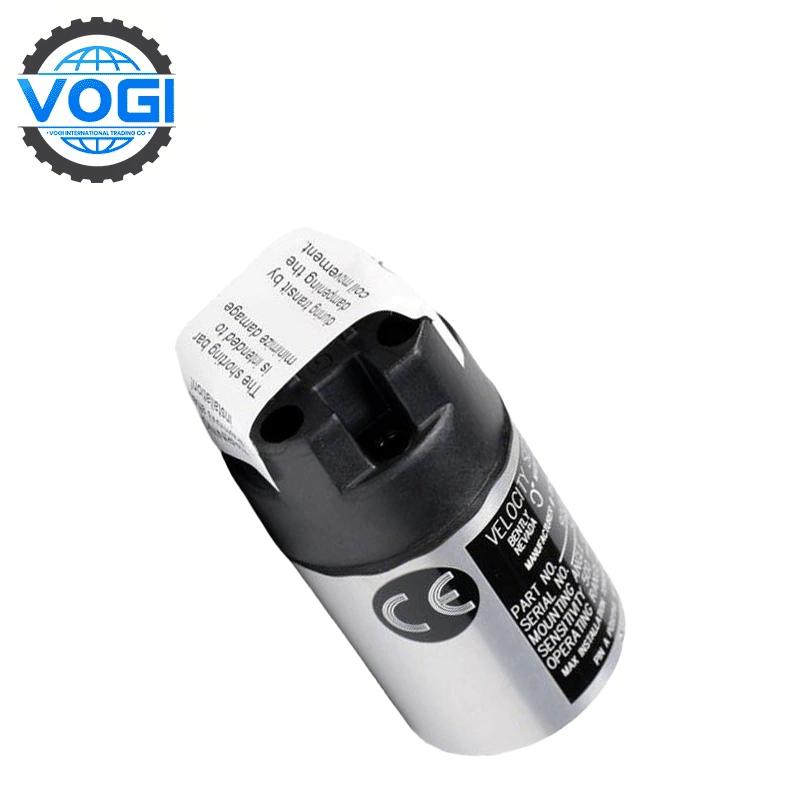
Bently Nevada 9200-06-05-05-00 Key Features
Moving-Coil Sensing Technology
The Bently Nevada 9200-06-05-05-00 employs a passive moving-coil design that generates a voltage signal directly proportional to vibration velocity without external power. This technology ensures high immunity to mechanical shock (up to 50 g peak on non-sensitive axes) and minimizes signal distortion during impulsive events like impacts. Unlike solid-state alternatives, it avoids electronic integration drift, making it ideal for long-term portable measurements in harsh industrial environments.
Terminal Block Top-Mount Design
The "05" suffix denotes a terminal block top-mount connector, eliminating integral cables and enabling field-replaceable wiring. This simplifies maintenance and allows custom cable lengths up to 305 meters. The M10x1 stud base requires tightening to 5.6 N·m for secure mounting at 0° ±100° orientation.
